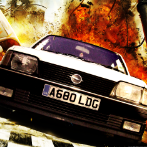
12 Initiation of diagnosis. n/a
13 Oxygen sensor No change in voltage/open circuit.
14 Coolant Temperature Sensor (CTS) Low voltage
15 Coolant Temperature Sensor (CTS) High voltage
16 Knock sensor 1 No change in voltage
17 Knock sensor 2 No change in voltage
18 Knock control unit No signal, Engine Control Unit (ECU) fault
19 RPM signal (crankshaft sensor) Incorrect signal
21 Throttle position sensor High voltage
22 Throttle position sensor Low voltage
23 Knock sensor module n/a
24 Vehicle speed sensor (VSS) No signal
25 Injector valve 1 High voltage
26 Injector valve 2 High voltage
27 Injector valve 3 High voltage
28 Injector valve 4 High voltage
28 Fuel pump relay Low voltage
29 Injector valve 5 High voltage
31 Engine RPM signal (crankshaft sensor) No signal
32 Injector valve 6 High voltage
32 Fuel pump relay High voltage
33 Inlet manifold pressure sensor Voltage too high
34 Exhaust Gas Re-circulation (EGR) valve Voltage too high
34 Manifold Absolute Pressure (MAP) sensor Low voltage
35 Idle Speed Control Valve (ISCV) Poor or no idle speed control
36 Incorrect RON/Octane setting Damaged RON plug or bad connection.
37 Engine self-diagnosis (fault code light) Low voltage
38 Oxygen sensor Voltage low (1990 model year on)
39 Oxygen sensor Voltage high (1990 model year on)
41 Vehicle speed sensor (VSS) Low voltage
41 1 gear ident switch (C20LET systems) Low voltage
41 EST Line coil cylinder 2&3 (M2.8/XEV systems) High voltage
42 Vehicle speed sensor (VSS) High voltage
42 1 gear ident switch (C20LET systems) High voltage
42 EST Line coil cylinder 2&3 (M2.8 / XEV systems) High voltage
43 Linear EGR system (XEV systems) Faulty
44 Oxygen sensor Air/fuel mixture too lean (weak)
45 Oxygen sensor Air/fuel mixture too rich
46 Air pump relay High voltage
47 Air pump relay Low voltage
47 Linear EGR Position (XEV systems) Faulty
48 Battery voltage Low voltage
49 Battery voltage High voltage
51 ECU Programmable memory PROM error, hardware failure
52 Engine check light; final stage (fault code light) High voltage
53 Fuel pump relay Low voltage
54 Fuel pump relay High voltage
55 Engine Control Unit (ECU) fault Renew Engine Control Unit (ECU)
56 Idle Speed Control Valve (ISCV) Short to earth
57 Idle Speed Control Valve (ISCV) Interruption
59 Inlet manifold valve 1 Low voltage
61 Fuel Tank Vent Valve (FTVV) Low voltage
62 Fuel Tank Vent Valve (FTVV) High voltage
63 Inlet manifold valve 1 High voltage
63 EST Line coil cylinder 2&3 (M2.8 / XEV systems) Low voltage
64 EST Line coil cylinder 1&4 (M2.8 / XEV systems) Low voltage
65 Carbon Monoxide (CO) potentiometer Low voltage
66 Carbon Monoxide (CO) potentiometer High voltage
67 Throttle valve switch - idle position switch Low voltage - switch not opening
68 Throttle Switch (TS) - idle contact Idle switch not opening
69 Air Temperature Sensor (ATS) Low voltage
71 Air Temperature Sensor (ATS) High voltage
72 Throttle Switch (TS) - full load contact High voltage - Full load switch not running
73 Air Flow Sensor (AFS) Low voltage
74 Air Flow Sensor (AFS) High voltage
75 Transmission switch - torque control Low voltage
76 Automatic Transmission (AT) torque control Engaged long, ignition ****** long
79 Traction control unit Incorrect ignition/injector cut-off
81 Injector valve 1 Low voltage
82 Injector valve 2 Low voltage
83 Injector valve 3 Low voltage
84 Injector valve 4 Low voltage
85 Injector valve 5 Low voltage
86 Injector valve 6 Low voltage
87 Air Conditioning (AC) cut off relay Low voltage
88 Air Conditioning (AC) cut off relay High voltage
89 Oxygen sensor heater Low voltage
91 Oxygen sensor heater High voltage
92 Camshaft sensor failure (XEV systems) Faulty
93 Hall Effect Switch (HES) Low voltage
94 Hall Effect Switch (HES) High voltage
95 Hot start valve Low voltage
96 Hot start valve High voltage
97 Traction control unit - ignition/injection cut off Incorrect signal - high voltage
98 Oxygen sensor Open circuit, wiring break
99 Code unknown n/a
113 Turbo boost control Boost presure high, out of range
114 Idle boost valve Above upper limit
115 Full boost pressure Below lower limit
116 Boost pressure Above upper limit
117 Wastegate valve Low voltage
118 Wastegate valve High voltage
121 Oxygen sensor 2 Lean exhaust, weak mixture
122 Oxygen sensor 2 Rich mixture/exhaust
123 Inlet manifold valve 1 Blocked
124 Inlet manifold valve 2 Blocked
132 Exhaust Gas Re-circulation (EGR) valve Incorrect signal
133 Exhaust Gas Re-circulation (EGR) valve 2 High voltage
134 Exhaust Gas Re-circulation (EGR) valve 2 Low voltage
135 'Check engine' lamp (fault code lamp) Low voltage
136 Engine Control Unit (ECU) n/a
137 Engine Control Unit (ECU) box High temperature
141 Secondary air pump Not enough air
142 Secondary air pump Air without pump
143 Immobiliser function in ECU No or incorrect signal
144 No immobiliser signal recived Faulty unit or break in wiring
145 Incorrect immobiliser signal received Faulty unit or break in wiring
- Read more...
- 0 comments
- 758 views